Bio-based biocomposite that biodegrades – complex or not?
The adoption of new sustainable materials is a prominent part in the set of solutions needed to tackle the global plastic waste problem. However, the characteristics and the ‘level of sustainability’ of these new materials vary greatly, even though they might appear similar to the consumer. In this blog we aim to explain the key elements of Sulapac materials, what they are designed for and what makes them a truly sustainable choice. We also seek to demonstrate how Sulapac® is different compared to some competing materials in the market.
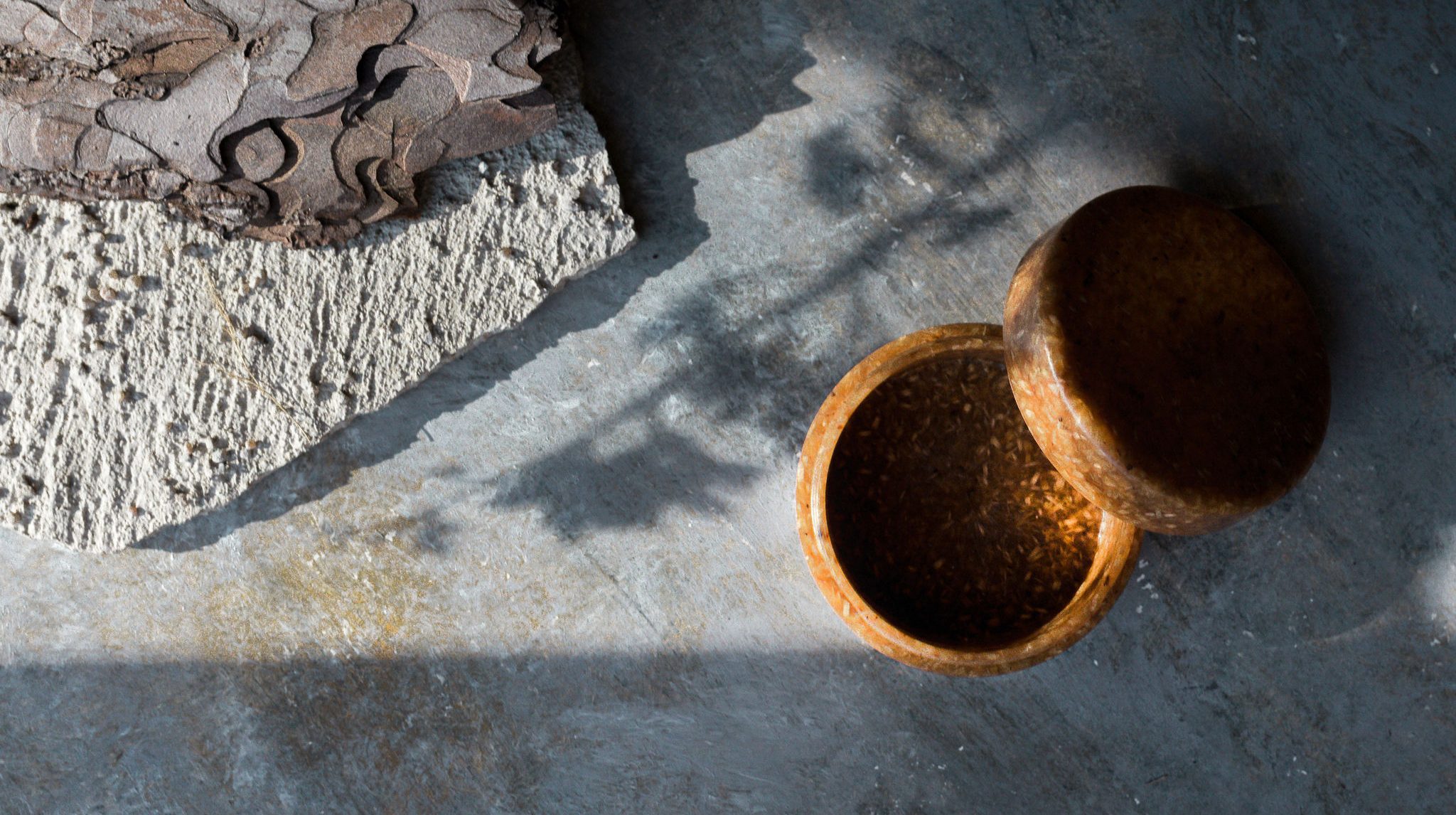
A Biocomposite
Sulapac® is a bio-based biocomposite that biodegrades. Composite is a combination of two or several materials, in which the materials function together, but are not dissolved or merged into each other. A composite typically aims at having one or more characteristic (such as strength or processability) which is better than any of its components has alone or more suitable for the application intended. A biocomposite, then again, is a composite, of which components at least one is bio-based.
Sulapac is mainly a combination of two material types: wood and a carefully selected biopolymers. Polymers are added in order to make the material more processable, so it can be used with existing plastic processing machinery. This is a great advantage, as it makes replacing plastic easy and commercially feasible: it saves resources and energy, as there’s no need to build new production lines.
Originates from plants
The group of biocomposites is versatile. Even materials that are combinations of traditional plastic and wood can be defined as biocomposites. In case of Sulapac, all our main components are bio-based and in certain recipes the bio-based content is 100%. Amazing, right? But because sustainability is at the heart of Sulapac, we’re aiming even higher. Our goal is to have only bio-based or recycled raw materials in all our recipes by 2025. This is documented as one of the key performance indicators in our environmental management system (ISO 14001).
Why bio-based?
Conventional plastics such as polyethylene (PE) and polypropylene (PP) are made from petroleum. In other words, they are fossil-based and made from non-renewable resources. Bio-based materials are made from renewable biomass sources. There are two main reasons why switching to bio-based raw materials is necessary: firstly, all fossil-based materials eventually contribute to CO2 burden that accelerates climate change, and secondly, with the increasing demand, fossil fuels will be soon get scarce. Fossil fuels are non-renewable and they cannot be regenerated quickly, whereas renewable biomass sources such as trees and plants re-grow fast, and during their growth, they absorb CO2 from the atmosphere. Sustainably grown bio-based options are better for the environment because they lack many of the harmful environmental impacts compared to the use of virgin fossil raw materials.
Conventional plastic is cheap to produce and has good qualities such as strength and toughness. The downside is that although the material is durable, it releases harmful microplastics already during use and especially if plastic waste is leaked into nature. These particles can persist in nature for hundreds of years. After use, only a fraction of all plastic – globally about 9% – is recycled.
Although the current recycling infrastructure favors conventional plastics, there are several recycling options for bio-based materials that biodegrade. As markets orient towards bio-based materials, these options will become more widely available, just like conventional plastic recycling. Sulapac material can be recycled via several routes. Currently the preferred recycling method is industrial composting, but it has been demonstrated that Sulapac Premium material could also be mechanically recycled: the properties of the material remain up to five recycling cycles. We also examine pyrolysis as a potential future recycling method.
When a fully bio-based material is incinerated for energy use, it emits bio-based CO2, which then cycles back to plants in the photosynthesis.
Sustainably sourced
Whether material is fossil or bio-based its sourcing matters. For example, if you accept wood which comes from conservation areas it can no longer be considered renewable. Our wood ingredient originates from sustainably managed Nordic forests. Moreover, it comes from industrial side steams, which means we use wood chips that would otherwise most likely be burnt for energy.
All our raw materials are sourced according to the principles of sustainable sourcing which are put to place to ensure the environmental responsibility but also the social responsibility throughout the entire supply chain.
Full biodegradation
Biodegradation refers to the biological process where naturally occurring microorganisms digest material into water, carbon dioxide and biomass. Polymers that biodegrade can be either bio-based or fossil-based.
All Sulapac components biodegrade fully which means that Sulapac materials do not accumulate in nature. Polymers that don’t biodegrade – the components of traditional plastic – then again, remain in nature for hundreds of years. Due to erosion, UV light, and weather conditions they disintegrate into micro- and nanoplastics, which cannot be digested by nature’s organisms.
Some bio-based plastics, which can be manufactured for example from sucrose, starch or cellulose, also may not biodegrade. This is because their chemical structure is identical to that of petroleum-based plastic. When you come across the term ‘bioplastic’, without further information, you can’t tell if it biodegrades or not.
Biodegradation speed and conditions vary
The term biodegradable itself is tricky. Some materials biodegrade in an industrial compost, but not in nature. Yet they can be claimed to biodegrade. We think that for many applications biodegradation in controlled conditions is not enough, but the material needs to be digested in a defined timeframe by naturally occurring microorganisms as well. This view is justified, until we see a radical change in human behavior and materials are no longer discarded or get leaked into nature. Furthermore, microplastic emissions may take place due to abrasion during the use of products. If the particles are resistant to biodegradation they can accumulate in nature or in humans. We have paid special attention to prevent the creation of permanent microplastics and tested that the biodegradation of Sulapac materials takes also place in marine conditions, which is the most difficult environment for the process.
In some cases, a material may biodegrade in nature, but the process takes several decades, and hence the material can accumulate. Plain PLA, a well-known bio-based plastic, is an example of this kind of materials.
Certified and safe
Composting is one way to recycle products or packaging that biodegrade. Certificates for both home composting and industrial composting exist. An item certified as compostable is always tested in terms of biodegradability, but also in terms of ecotoxicity. This means that the quality of the end compost has been carefully analyzed by an independent third-party laboratory.
The European standard EN 13432 defines the requirements for industrially compostable packaging and how the tests must be carried out. Besides the EN 13432 testing, the environmental safety of Sulapac materials has been ensured by Daphnia magna (a tiny planktonic crustacean) ecotoxicity test. Sulapac Premium Plus material and the Sulapac straw are also Seedling certified.
What is Sulapac used for?
Sulapac materials are developed to replace traditional plastic in a variety of applications. We focus especially on applications in which biodegradability is a fundamental benefit. We have recipes that are perfect for straws and other single-use items such as cutlery and personal hygiene products. On the other hand, we have recipes developed for packaging, which are superb for premium brands in the cosmetic, jewelry and food sectors, for example.
Sulapac materials can also replace plastic in medium lifetime consumer goods categories, but when it comes to durable goods like surf boards or garden furniture, at this stage, Sulapac is not a recommended alternative.
We not only provide sustainable materials but also want to make sure that the end-product is better with Sulapac. Our mission is to accelerate a plastic waste-free future by offering a mass-producible yet sustainable, beautiful and functional alternative to traditional plastic.
Find out more about our bio-based biocomposites that biodegrade on our portfolio!
Laura Tirkkonen-Rajasalo
Director of Quality Assurance and Regulatory Affairs, Co-Founder
Edited 27.10.2021
Sulapac accelerates a plastic waste-free future with sustainable materials that are beautiful and functional. Like nature. Sulapac® is an award-winning, patented, bio-based material innovation for circular economy. Forerunner companies around the world, along with CHANEL, have chosen Sulapac. The Helsinki-based company’s investors include CHANEL and Sky Ocean Ventures. Sulapac was ranked one of Europe’s 100 hottest startups by WIRED UK in 2018, 2019 and 2021, and one of the Nordic startups to watch in 2021 by Sifted, backed by the Financial Times.Join the forerunners. Together we can save the world from plastic waste.