Your ultimate guide to sustainable 3D printing
The popularity of 3D printing is constantly increasing. That’s hardly a surprise – it’s fast, efficient, and affordable. 3D printing can also cut down on material waste, bringing sustainability benefits. Let’s look at how 3D printing works and how bio-based materials are changing the sustainable manufacturing game.
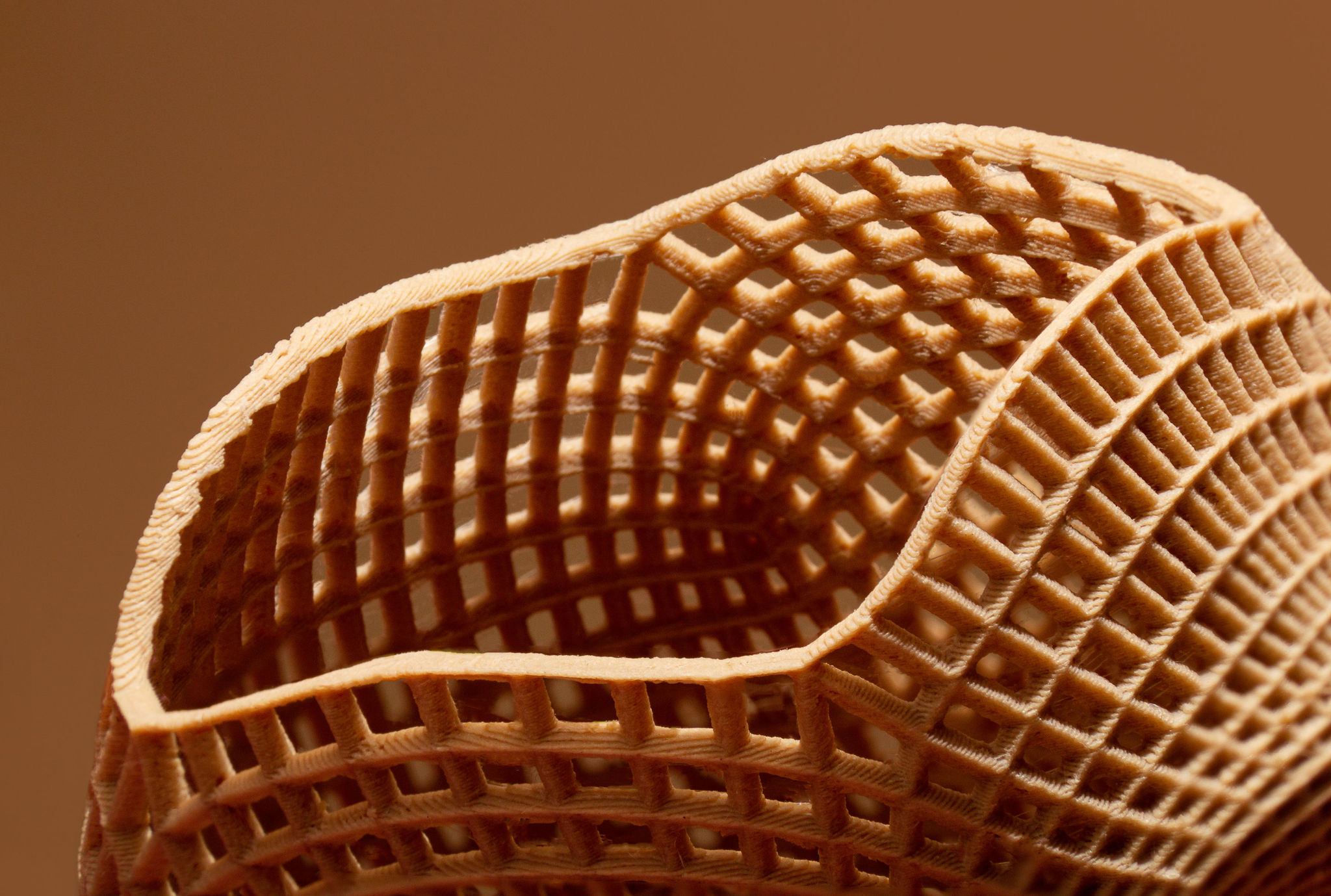
3D printing: how does it work
3D printing is the process of producing three-dimensional items based on digital models. Objects are created by adding layer after layer of material. The process will typically begin with the creation of a 3D model. The model is then sliced into thin layers, each being a 2D cross-section of the item. Next, the printing material is selected, and the 3D printer is prepared. Once that’s done, printing can begin. The object is built layer by layer, with the printer following the instructions from the sliced model. Finally, post-processing takes place. This could involve sanding or cleaning to give the finished surface the desired appearance.
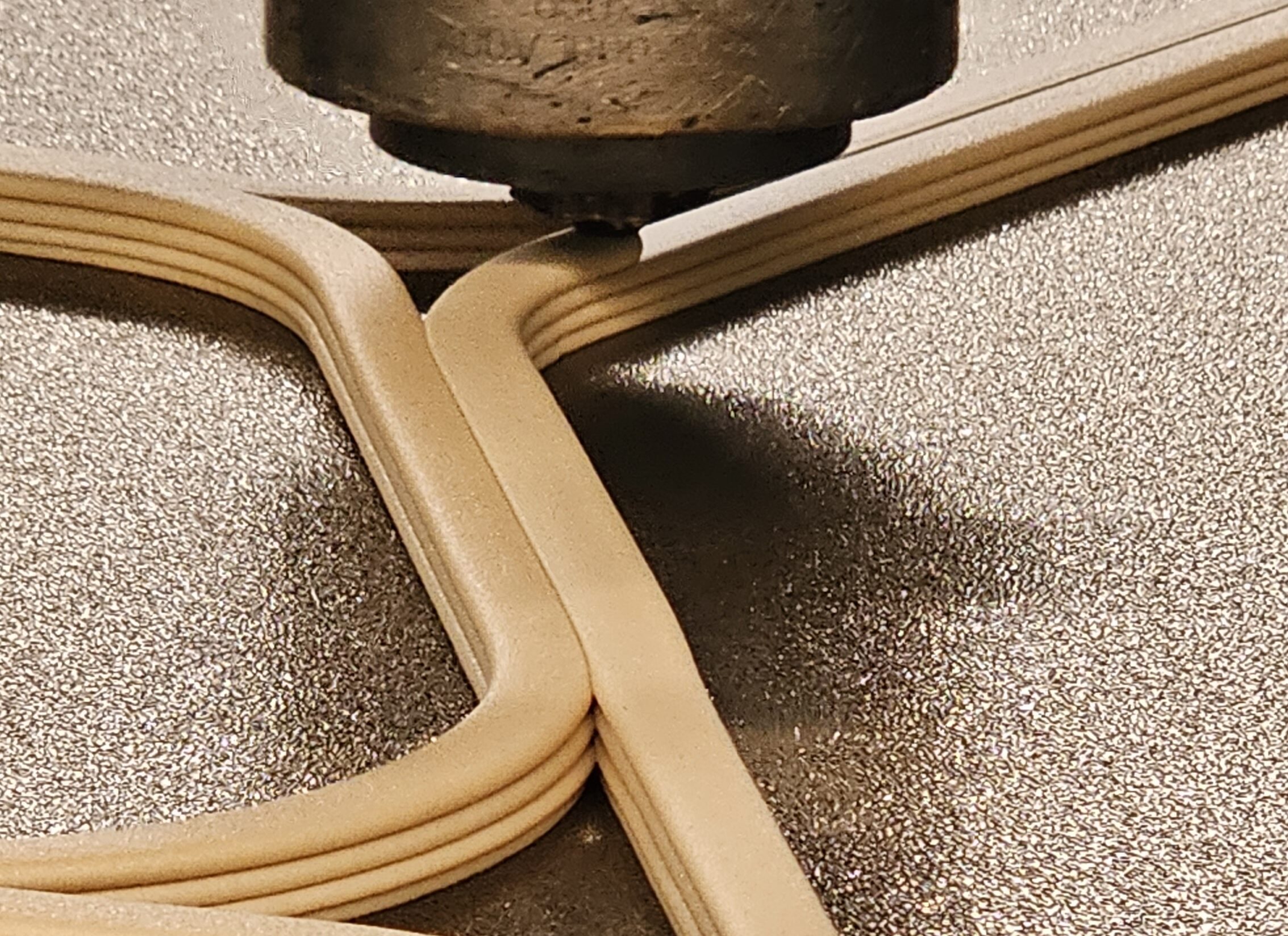
So, what’s additive manufacturing?
You’ll often hear 3D printing referred to as additive manufacturing. This refers to the layer-by-layer process used when printing a three-dimensional object. The process is ‘additive’ because material is incrementally added until an entire object is formed.
Additive manufacturing contrasts with traditional manufacturing processes, such as molding or machining. These often involve subtracting materials to achieve the desired shape of an item.
Additive manufacturing is a highly versatile manufacturing method. It can create challenging shapes and structures with precision and using a wide range of materials. And compared to traditional subtractive methods, it reduces material waste, meaning it’s a more sustainable process.
There are a variety of additive manufacturing printing techniques out there. Let’s focus on one of the most common techniques: fused deposition modeling (FDM), which is widely used across industries and by consumers as well.
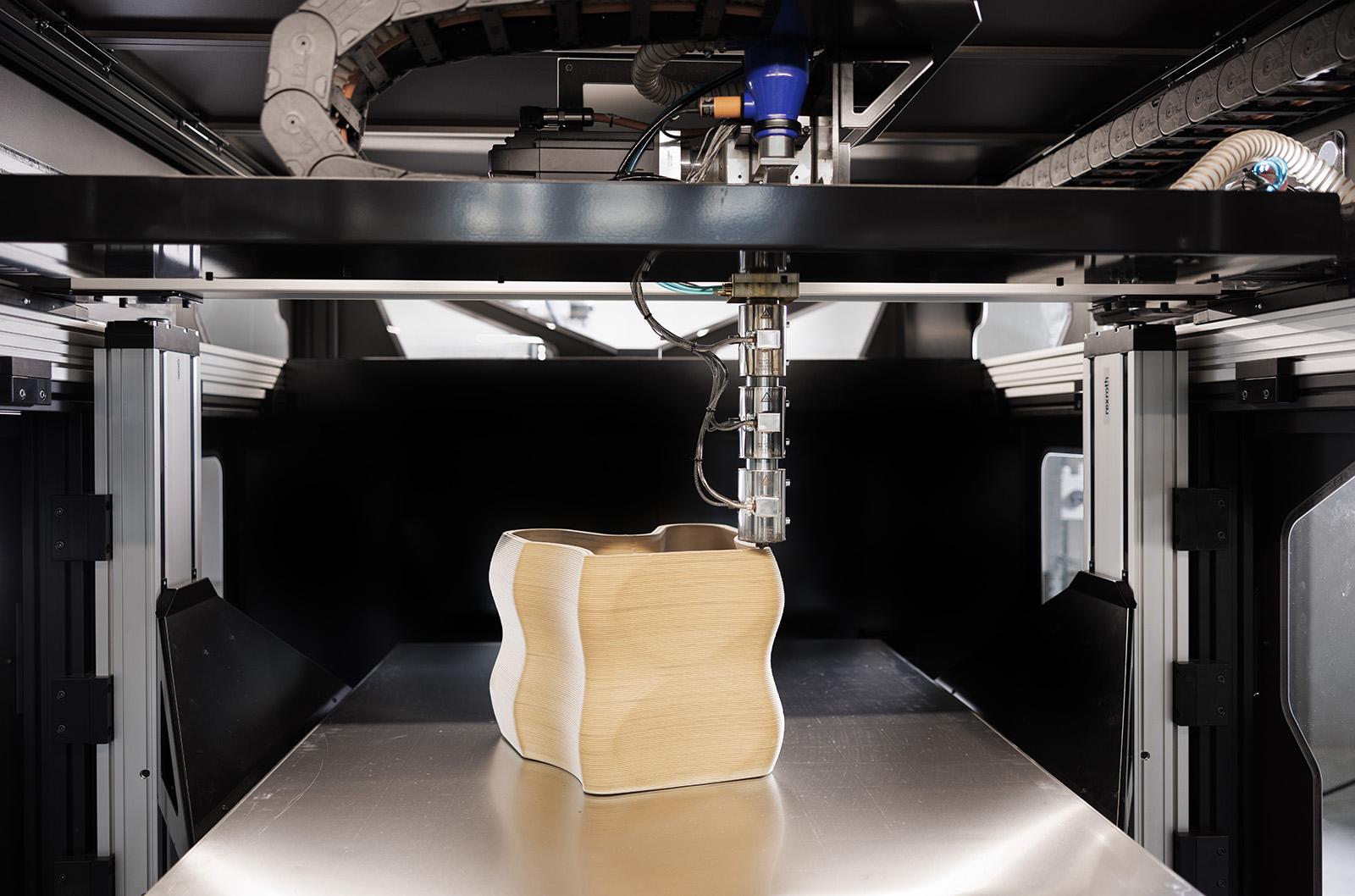
Fused deposition modeling (FDM)
Fused deposition modeling (FDM) is an extrusion-based additive manufacturing method where the material is extruded through a nozzle, one cross-section of a layer at a time. These layers are joined together to create 3D objects. Layer thickness determines the quality of the 3D print.
There are many benefits to FDM. It’s easy to use and versatile. It’s cost-effective compared to other additive manufacturing printing technologies. The benefits of FDM also include large build volume, and the ability to create products with good mechanical strength and durability.
FDM uses thermoplastics as feedstock (the raw material used in 3D printing to create an object), usually in the form of filaments or pellets (granules). Next, let’s look at the differences between these two.
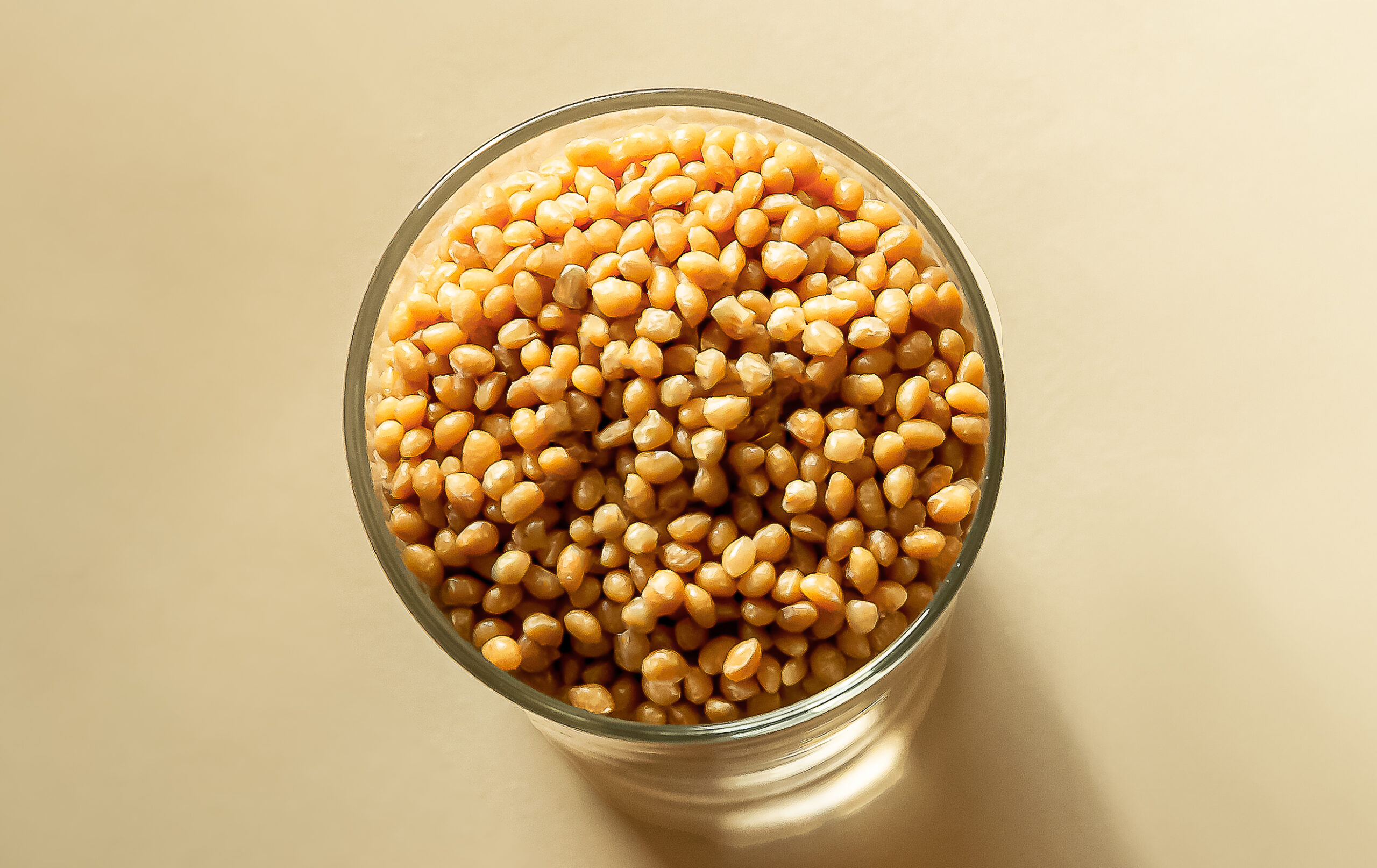
Filament printing versus printing directly from granules
The filament used in 3D printing is a long, narrow strand of thermoplastic wound onto a spool. This thread-like spool is fed into the 3D printer, where it’s melted and then deposited in layers. These layers are what the 3D object is built from. A core benefit of filament printing is the easy control it allows over materials.
Printing directly from granules or pellets is a technique most often applied in large-scale 3D printers. Granules and pellets are tiny particles of material, typically of uniform size and spherical or cylindrical in shape used as feedstock in 3D printing. Inside the 3D printer, granules are superheated before extrusion, where they are deposited in layers that eventually create the object.
Printing directly from granules or pellets is cost-effective, especially for industrial-scale printing as it allows higher printing speed. It also enables a wider range of material choices. Granules can be easier to transport and handle than spools of filament. The ability to print continuously is another advantage.
You may also come across the term ‘shredded material’ when it comes to 3D printing feedstock. It refers to recycled or discarded 3D printed objects that are broken down into small pieces for reusing as filament or feedstock in the printing process. Shredded material will often be used in highly specialized 3D printers built to handle uneven materials.
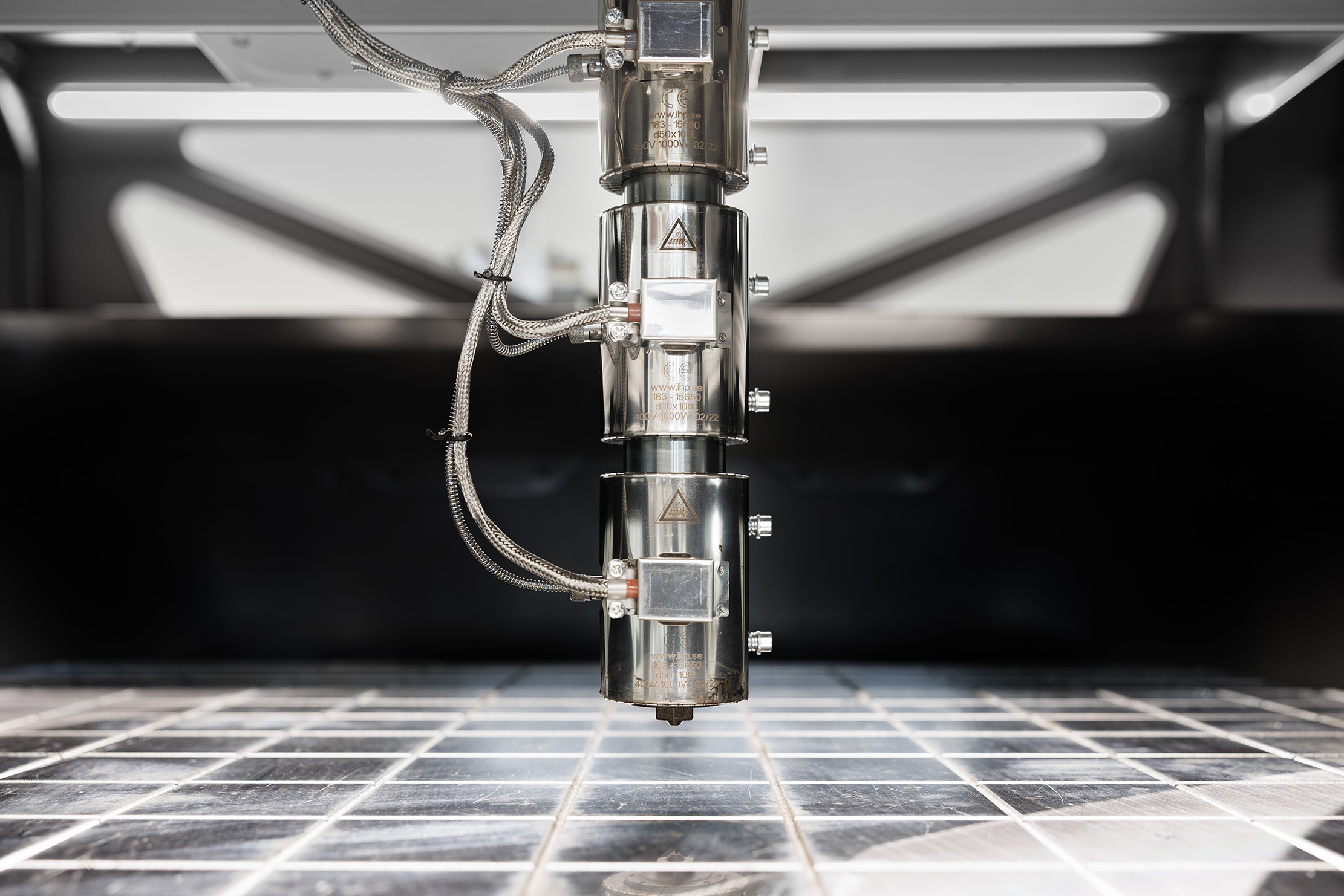
Commonly used feedstocks in FDM 3D printing
3D printing uses a wide range of raw materials. They include plastics, ceramics, resins, metals, sand, textiles, biomaterials, glass, and food. Let’s examine the material group most often used in FDM 3D printing – thermoplastics.
Acrylonitrile butadiene styrene (ABS) is a popular thermoplastic in 3D printing thanks to properties like strength, temperature resistance, and material versatility. But there are a few downsides. Notably, ABS is oil-based and unsuitable for food contact. It is extremely difficult to recycle. ABS can also pose difficulties in the 3D printing process, such as deforming when not printed on a heated surface.
Polylactic acid (PLA) is another popular thermoplastic used in 3D printing. It’s easy to use and widely available. It’s also biodegradable. However, temperature sensitivity is a consideration with PLA, as the material cannot cope with prolonged heat exposure.
Polypropylene (PP) is a thermoplastic known for chemical resistance, strength, and high density. Unlike PLA, PP has good heat resistance. But there are challenges associated with PP. Its poor layer adhesion means that the strength and durability of printed items may be negatively impacted. PP’s higher shrinkage during post-processing can also lead to warping in printed parts.
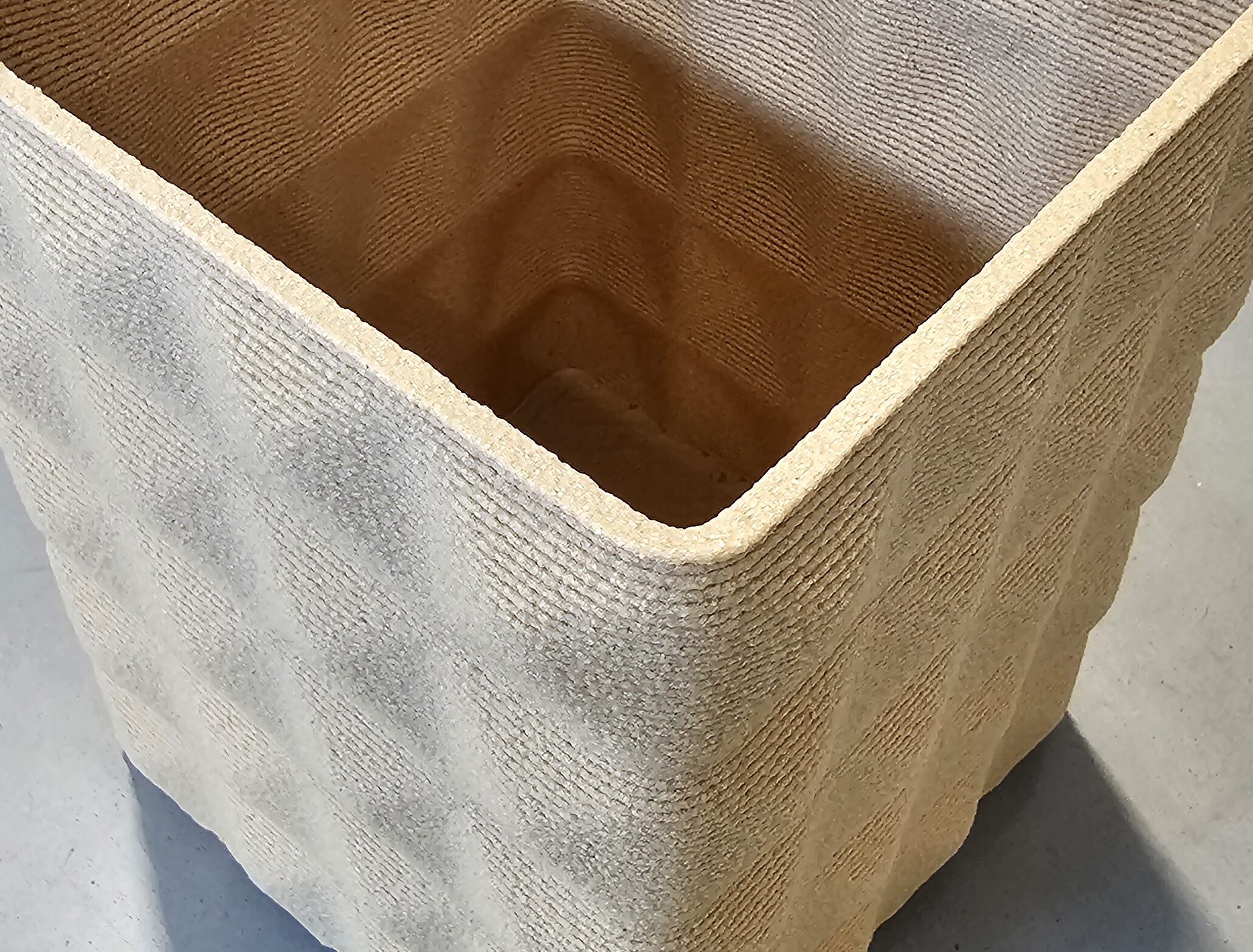
Sustainable feedstock alternatives for fused deposition modeling
In addition to the commonly used thermoplastics, which all have issues worth considering, from negative environmental impacts to 3D printing challenges, there are now novel, renewable material alternatives in the market that can offer significant sustainability benefits while securing an effective printing process and advanced mechanical properties.
Sulapac Flow 1.7, Sulapac Luxe and Sulapac Universal Heat materials are not only bio-based, biodegradable and recyclable by design, but also enable easier 3D printing. Sulapac materials are suitable for printing directly from granules as well as filament extrusion.
Sulapac’s thicker print layers mean faster printing – but without compromising on printing quality. In fact, Sulapac can be printed twice as fast as PLA. And unlike PLA, Sulapac Universal Heat 30 is designed to withstand high temperatures.
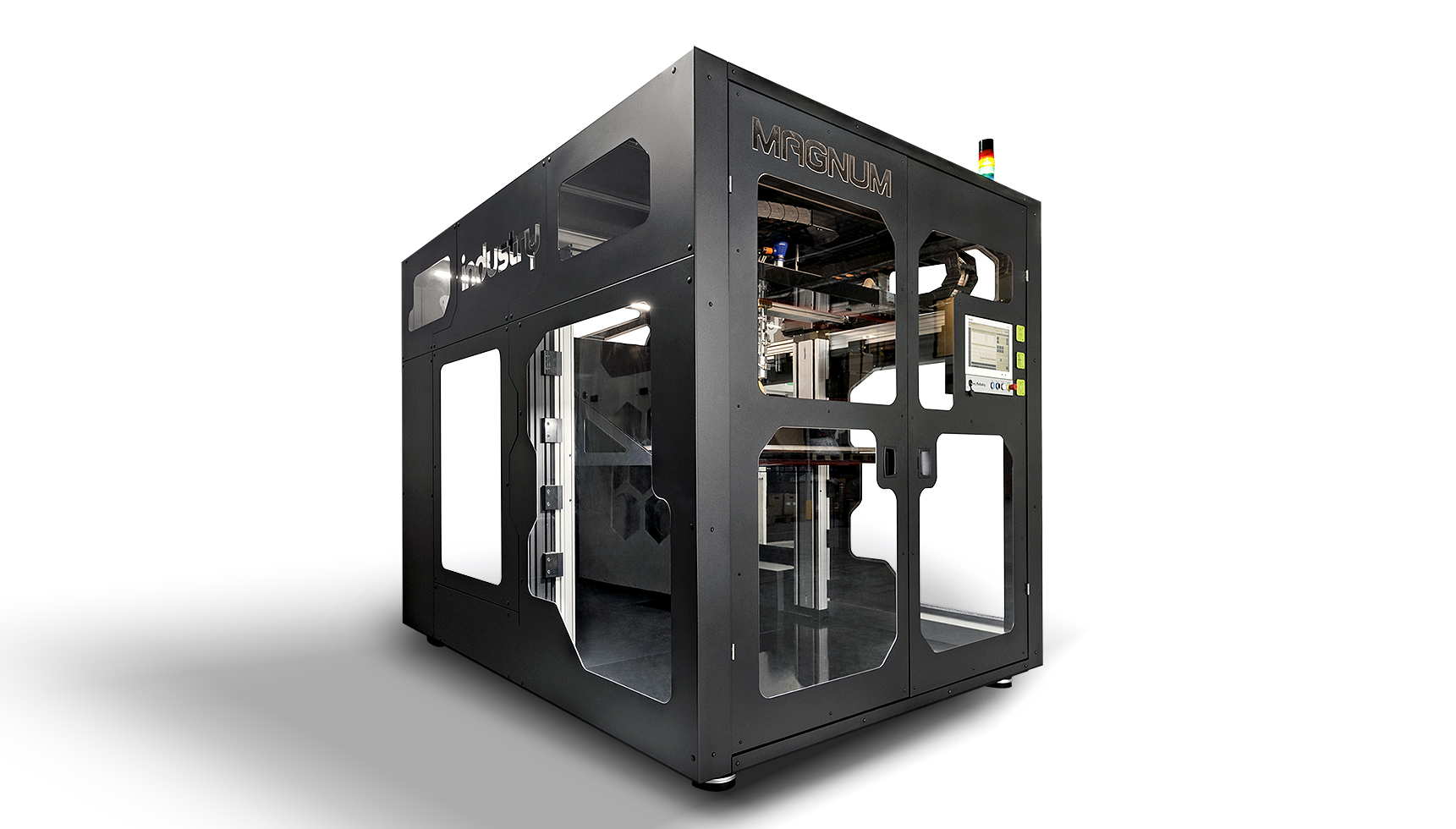
Sustainable manufacturing redefined: Large-scale 3D printing with Sulapac materials
3D printing is revolutionizing how large objects are created across a variety of industries including architecture, art, marine engineering, and automotive and aerospace manufacturing.
Large-scale 3D printing, sometimes called macro or giant 3D printing, pushes 3D printing technology to the limits to produce items with size beyond what conventional 3D printers can do. Industrial-scale printers may be room-sized or fill entire printer farms.
MAGNUM by The Industry is an example of a large-scale 3D printer, which is used to create a wide range of applications, including furniture and interior design objects, pressure molds, concrete molds, and molds for injection molding. For example, the Sulapac Flow 1.7 is among the recommended feedstock materials for MAGNUM printers.
The Industry’s customers can either purchase Sulapac material to be used in their MAGNUM printer in-house or order large-scale 3D printed items made of Sulapac from The Industry.
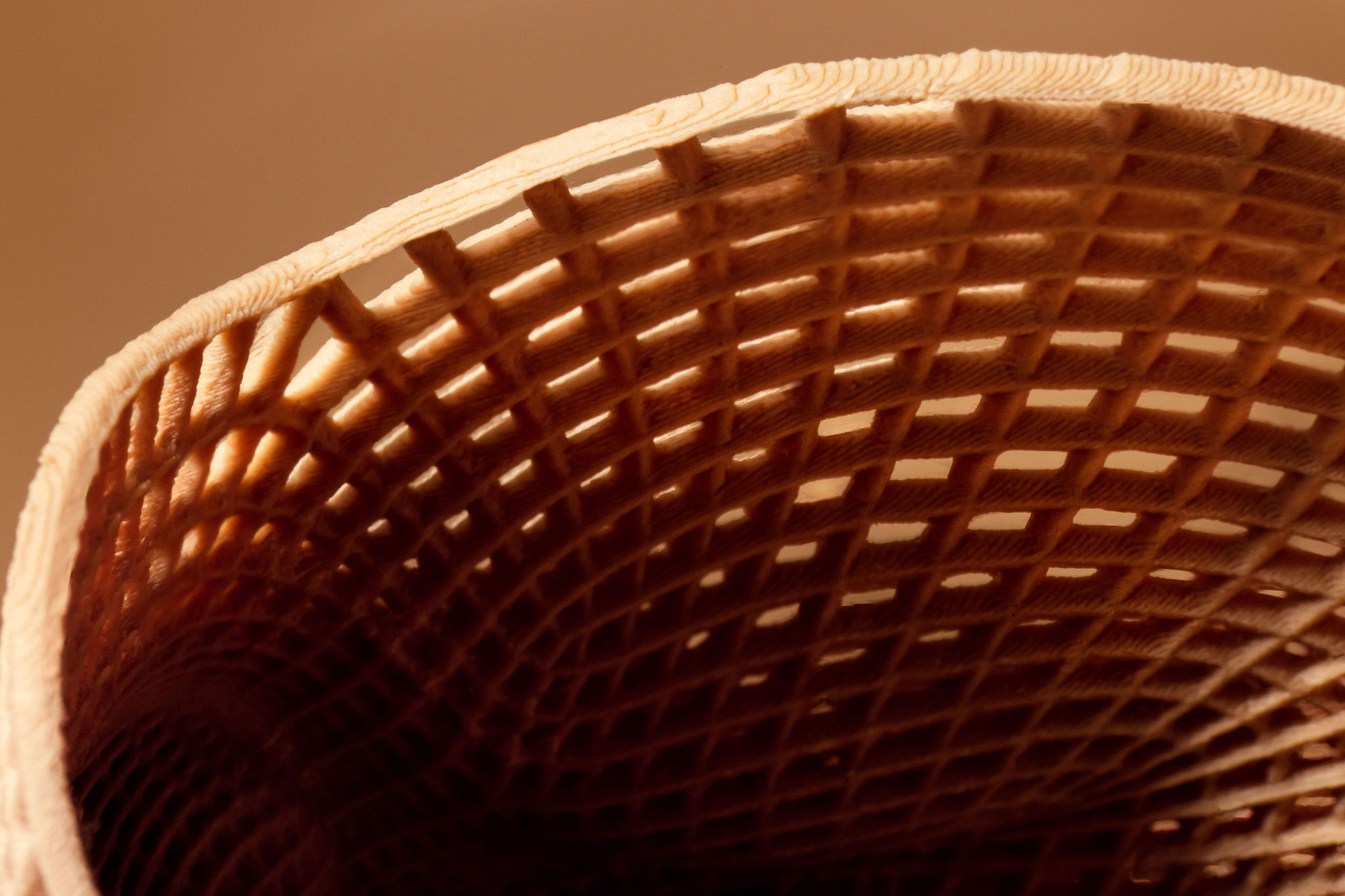
Interested in using Sulapac in 3D printing? Contact us and let’s get you some samples!