Towards sustainable circular future: Recycling of biobased biodegradable materials
Plastics account for about 4% of the global greenhouse gas emissions. In addition, they are a source of permanent microplastics throughout their lifecycle. It is already common knowledge that microplastics pose a fundamental threat to ecosystems and human health. Less known is the fact that there is a technically and commercially feasible solution to address both of these challenges at once: a circular model where biobased biodegradable materials are efficiently recycled enabling the biogenic carbon to stay in the loop almost endlessly. Let’s dive into the circularity of biobased biodegradable materials and discuss the actions needed to unleash their full potential.
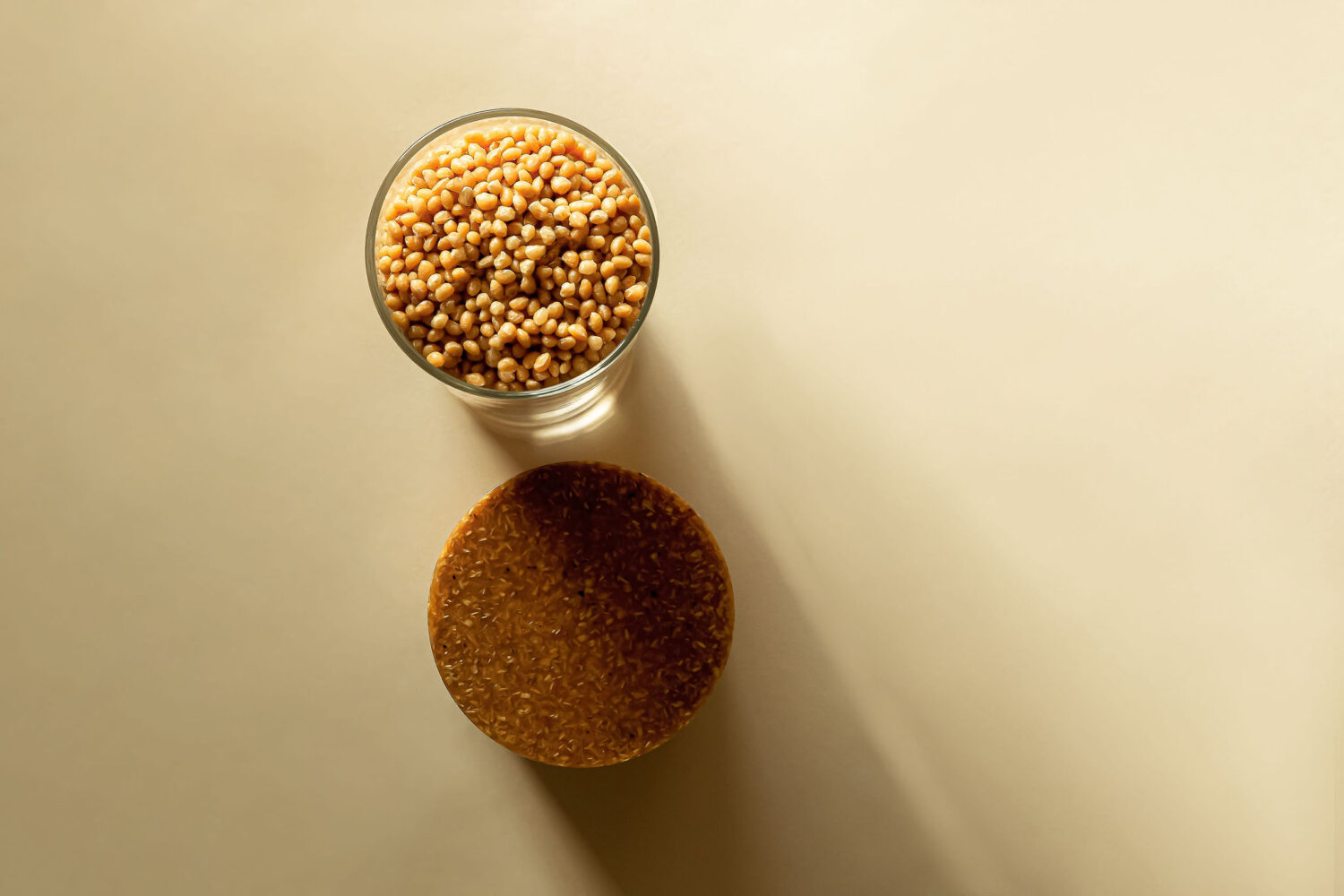
The ever-increasing plastic production inexorably leads to increasing amounts of plastic pollution. Currently, at least 14 million tons of plastic end up in the ocean every year, and all that eventually degrades into microplastics. Microplastics pose a fundamental threat to ecosystems and human health. Furthermore plastics share of the global greenhouse gas emissions is estimated to reach 19% by 2040. A radical shift on a systemic level, is the only way forward.
Why mechanical recycling is a false hope?
Recycling is often given as the silver bullet to the plastic crisis. But it’s not. Recycled conventional plastic is still a source of permanent microplastic. Even the recycling process itself is a source of permanent microplastic.
Moreover, no matter how hard we recycle, we can’t break free from our oil dependency, as the mechanical recycling of conventional plastics requires the input of new oil-based plastic during each cycle of recycling. Conventional plastic can be currently recycled at best once or twice before the material quality decreases – resulting in perpetual demand for virgin plastics. According to the Ellen McArthur Foundation’s New Plastic Economy report, around 80% of recycled PET bottles, for example, are turned into polyester fibers for carpet, clothing, and other non-packaging applications. Other large applications for open loop plastics recycling are low-value applications such as ‘plastic lumber’, plastic pipes, and waste collection bags, according to the report. “These applications are typically not (economically) recyclable after use, so open-loop recycling today often adds just one additional use cycle rather than creating a truly circular model.”
According to the International Energy Agency, petrochemicals are set to be the largest driver of world oil demand in 2050.
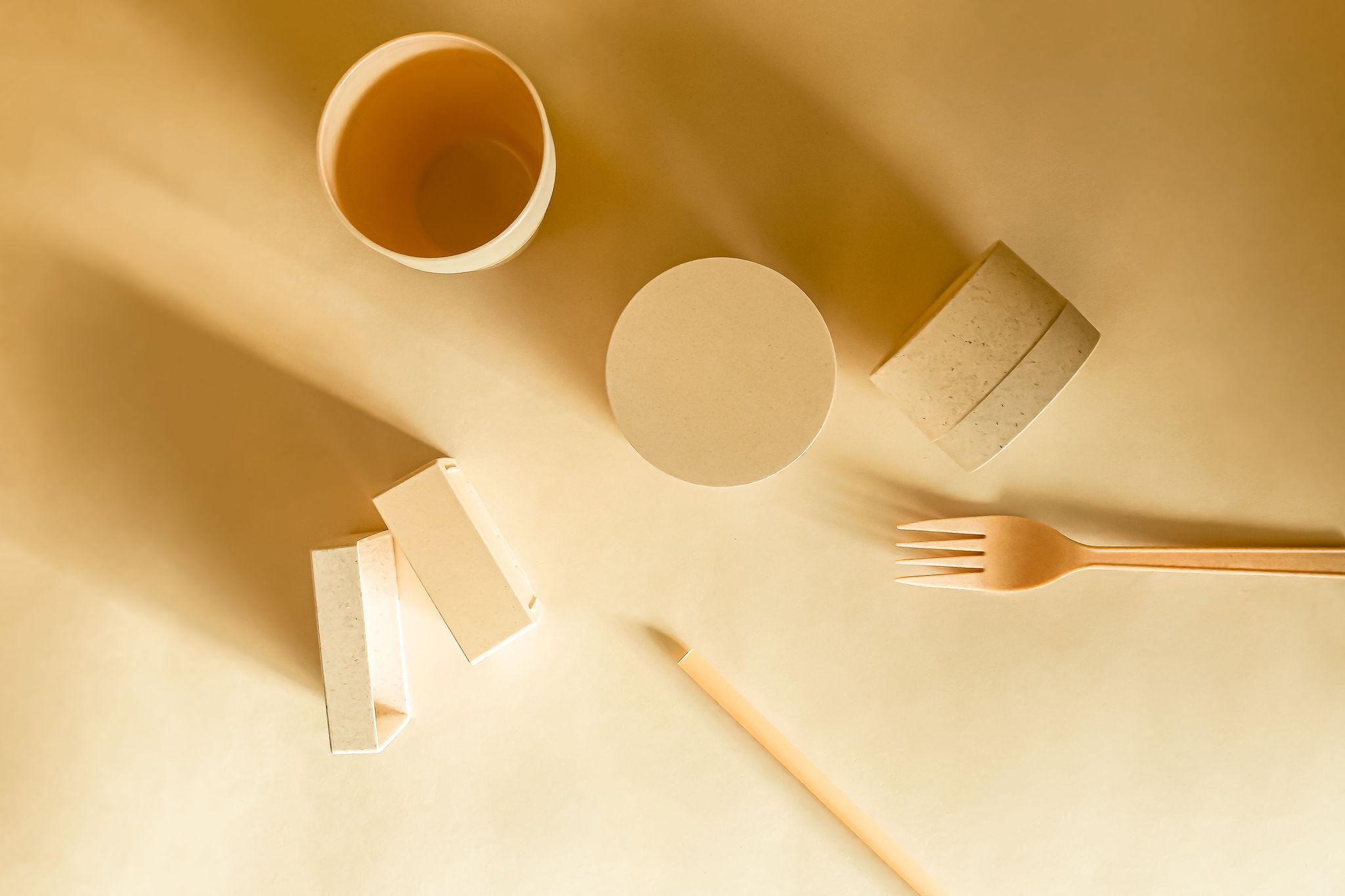
Bio-based, biodegradable, and recyclable materials – the ultimate solution
The only way to cut our dependency on oil and put a stop to microplastic pollution is to replace conventional plastic with biobased and biodegradable materials, that leave no permanent microplastics behind during any stage of the product life cycle.
For this material group to be a viable and sustainable solution in the long term, you need to be able to recycle them efficiently. The use of recycled biopolymers lowers the carbon footprint of Sulapac and similar materials even further and removes the potential negative biodiversity impacts related to the land use to grow crops utilized in bioplastic production.
Various advanced chemical recycling technologies for biobased biodegradable materials exist and there are players who are already collecting and recycling biodegradable bioplastics like PLA and PHA on a pilot scale. Also, some of Sulapac’s material grades have already been verified chemically recyclable. For example Sulapac Solid has the validation for LOOPLA technology.
However, to reach the full potential of these and similar kinds of eco-materials, an efficient and encompassing (chemical) recycling infrastructure needs to be developed worldwide.“Replacing conventional plastic with biobased biodegradable materials and establishing an effective recycling system for this material group is the key for a cleaner future; It enables us to cut our dependency on oil, eliminate microplastic pollution and tackle global warming,” states Suvi Haimi, CEO and Co-founder of Sulapac.
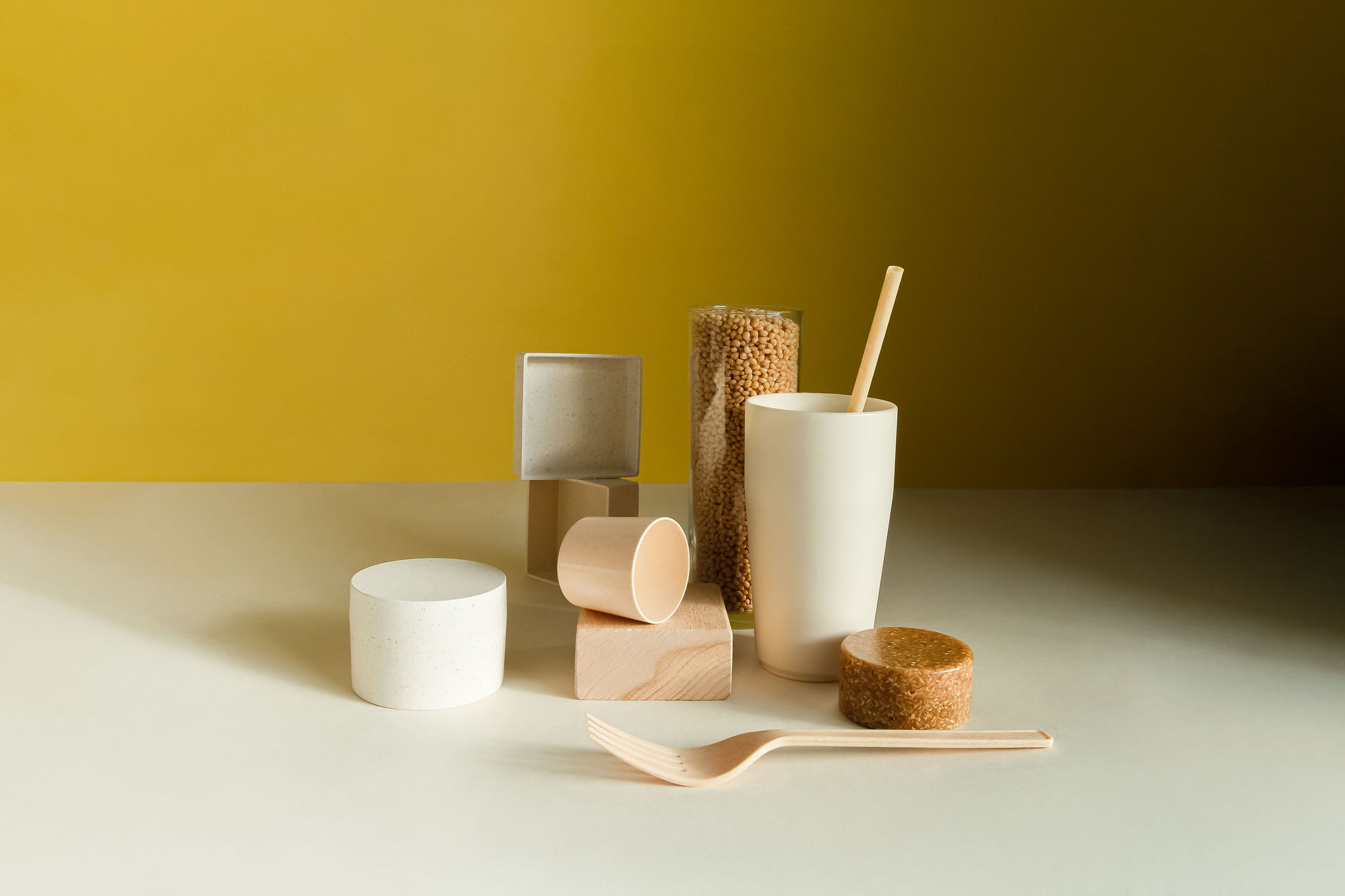
Why chemical recycling is the way of the future
Chemical recycling is a group of technologies aimed at breaking down polymers into their original building blocks which can then be used to produce virgin-quality raw material for new applications. Chemical recycling technologies take advantage of chemical processes including hydrolysis, catalysis, and depolymerization.
Depolymerization (polymer-to-polymer process) is the preferred method to recycle Sulapac materials. It is a highly efficient process; the yield for biobased biodegradable materials cab be as high as 95%. In case of conventional plastics, the yield ranges between 30-80%.
Furthermore, the chemical recycling process of biobased biodegradable materials requires far less energy than the chemical or mechanical recycling of conventional plastic, and there are no microplastics produced during the process and no fossil raw material input needed. Finally, it can take place without solvents or acids that are harmful to people and the planet.
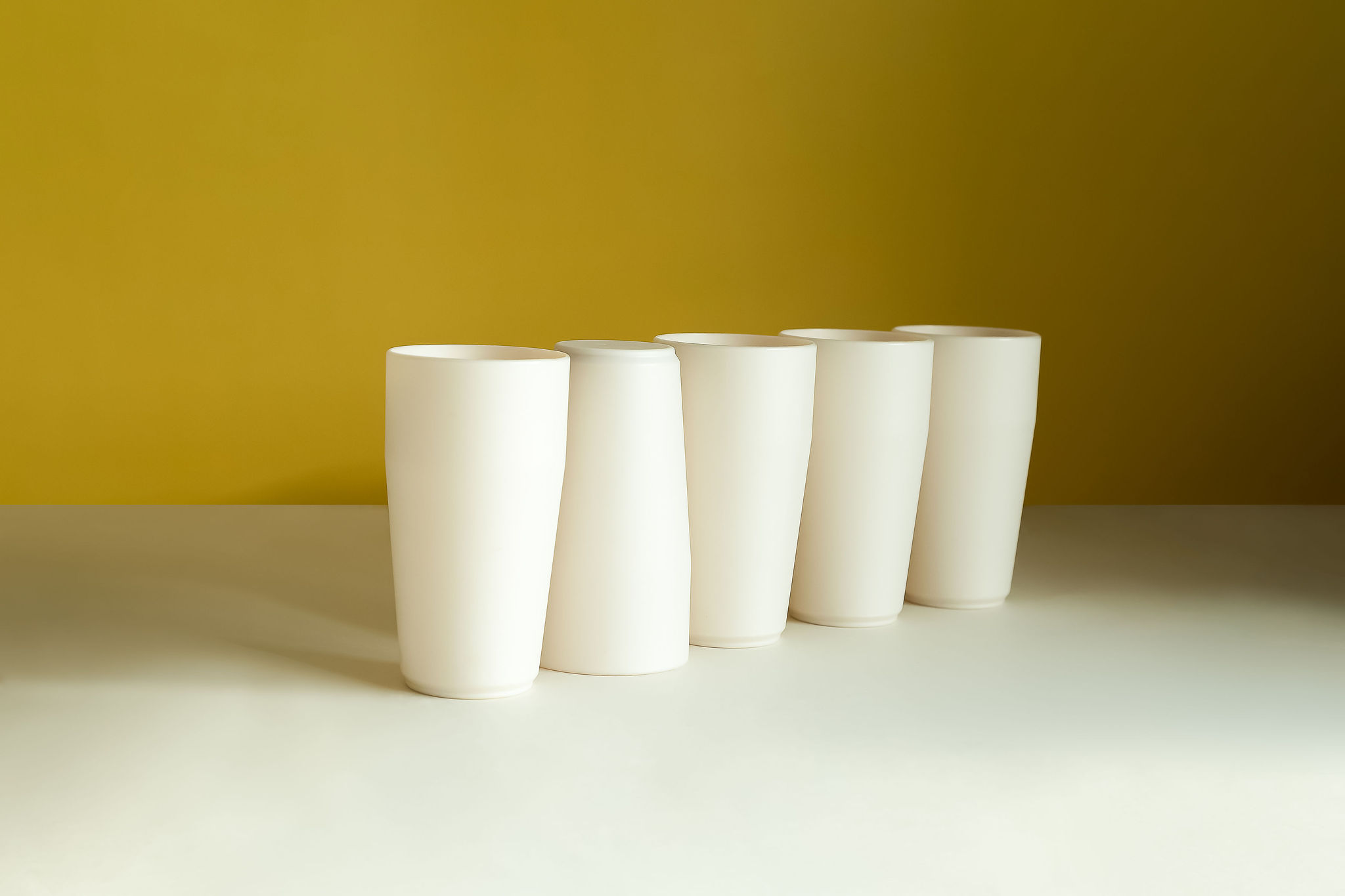
Pressure for a proper recycling infrastructure
Already today Sulapac can provide materials that incorporate high percentages of recycled content: up to over 70% recycled biopolymer content in selected material recipes. Our goal is that all our main raw materials will be waste-based or originating from side streams within the next five years.
To secure enough recycled content in the long term, it is essential to get the waste management companies to sort out Sulapac and other biodegradable biobased materials from mixed waste streams. Field tests have already verified that Sulapac materials can be collected and sorted out of a mixed waste stream with the NIR (Near-Infrared) technology.
It should be noted that Sulapac is not the only commercial material in this field; the production of biodegradable biopolymers is expected to reach over 3,5 million by 2027. Hence, it the collection of bioplastics as a separate waste stream will, at least to certain extent, also take place, with PLA and PHA as the first bioplastics expected to become recyclable at scale. Sulapac materials are designed in a way that enables them to be collected, sorted, and chemically recycled (polymer-to-polymer process) as part of the same waste streams as PLA and PHA.
Industrial investments in recycling technology and infrastructure for biobased biodegradable materials in the EU region are taking place as we speak. For example, a commercial scale facility in France will start its operations within the next couple of years. The investments are mainly driven by strong economic incentive as the demand for recycled biodegradable biopolymers continues its rapid growth.
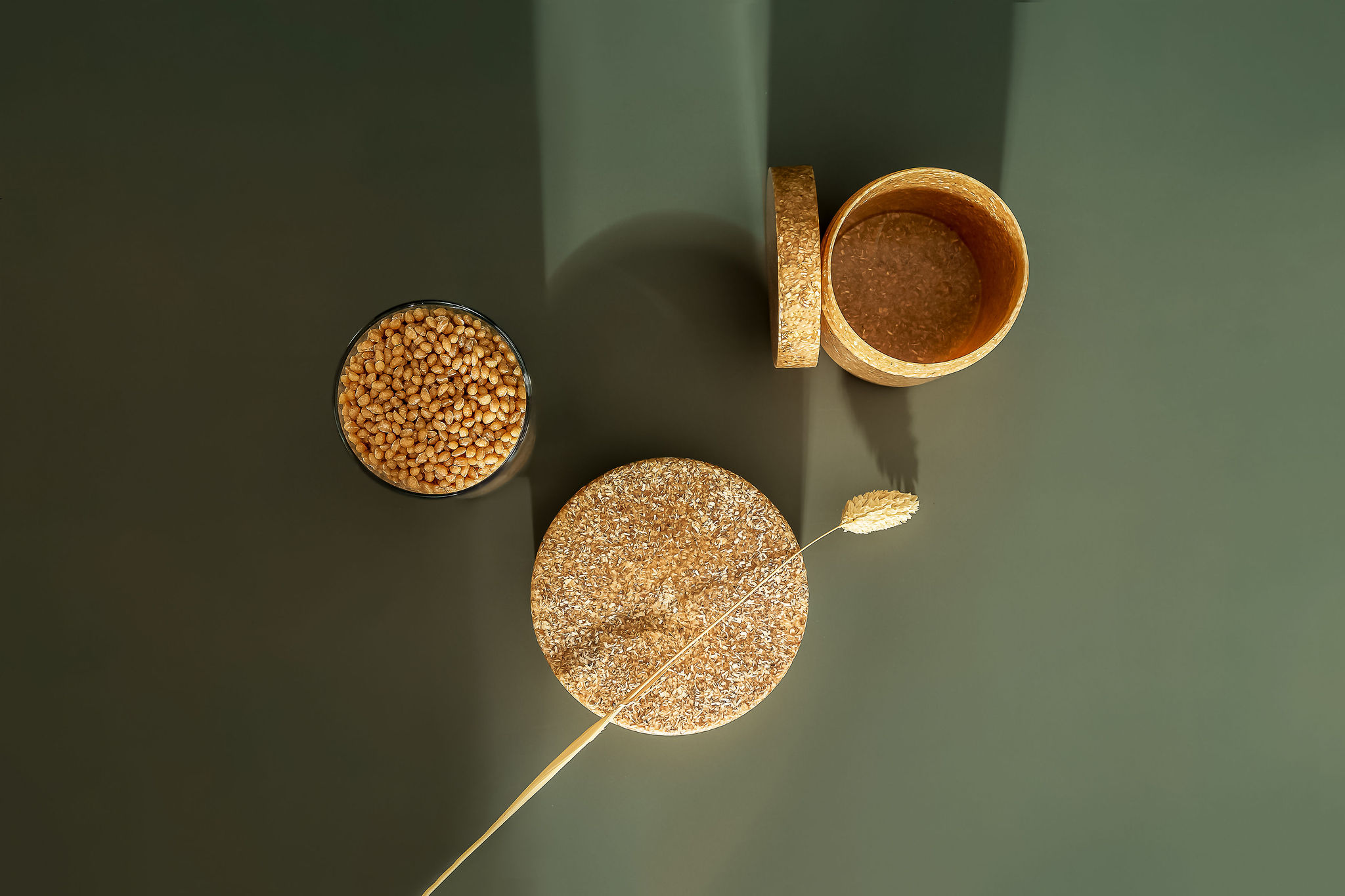
Accelerating the systemic change: Sulapac closed-loop model
It takes time before there’s an encompassing and efficient recycling infrastructure for biobased biodegradable materials that covers the entire EU region. But there are things that can be implemented already today to accelerate the change.
For example, Sulapac has launched closed loop pilot projects, an example of which is the collaboration with Kamupak and Lassila & Tikanoja. As one of the first events in the world Slush adopted the closed loop model with Kamupak’s cups made of Sulapac for their 2023 event in Helsinki. The cups are reused several times and in their end of their usage life, they are collected by Lassila & Tikanoja. Sulapac manages the recycling and utilizes the recyclate to cretae new high quality material. The purpose of the closed loop pilots is to demonstrate the feasibility of collecting and recycling biodegradable biobased materials as well as to make a concrete impact.
The Sulapac Closed Loop Platform is available also to selected cosmetic customers and for example event operators during 2024. By joining The Sulapac Closed Loop Platform companies can be true pioneers of the circular bioeconomy, secure recycled content to meet their sustainability targets and engage their customers in a unique way. If you are interested in hearing more, don’t hesitate to contact our sales team. Together we can close the loop for good.
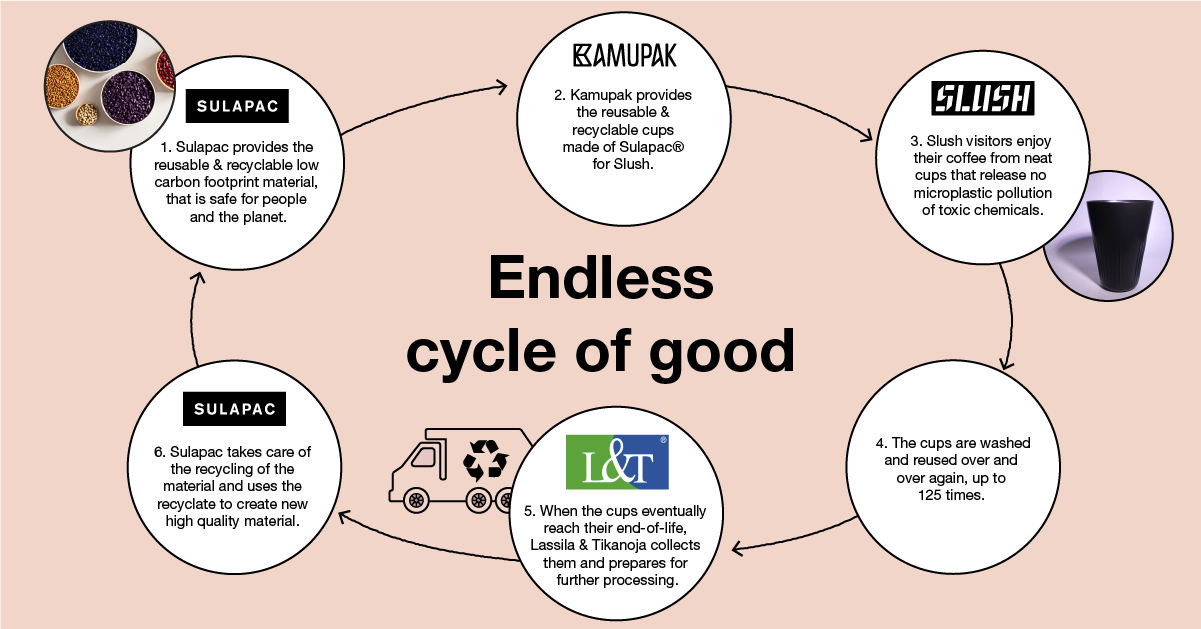
We have all the pieces – are we able to connect them?
Large-scale adoption of biobased biodegradable materials and their effective chemical recycling are central elements in tackling microplastic pollution and global warming. It is evident that the recycling of conventional plastic will not solve these issues. Luckily, chemical recycling of biobased biodegradable materials is an efficient process for which technology already exists. Hence, building a recycling infrastructure for biodegradable biobased materials should be made a priority by the regulative and legislative authorities in the EU.
What we as individuals and companies can do to accelerate the systemic change, is to prioritize biobased and biodegradable materials, contact the local policymakers stressing the crucial nature and urgency of the issue, boldly speak the truth about the destructive effects of the oil-based economy, and launch and participate in recycling pilots for biodegradable biobased materials whenever the opportunity arises.
Sulapac Ltd accelerates the plastic waste-free future by helping companies replace conventional plastic with sustainable, beautiful and functional materials that are circular by design. The company was founded in 2016 by three scientists Dr. Suvi Haimi, Dr. Laura Tirkkonen-Rajasalo and Dr. Antti Pärssinen, and was ranked one of Europe’s 100 hottest startups by WIRED UK in 2018, 2019 and 2021. Investors behind Sulapac®, the award-winning, patented material innovation include CHANEL and Sky Ocean Ventures.