Traceability and segregation in Sulapac production
Quality assurance is crucial for maintaining a high standard of our materials and ensuring customer satisfaction, as well as a legal requirement when it comes to food contact materials, which is why it has been incorporated into the way we operate, from raw material selection to production and delivery. Quality is not an exclusive property of our quality team, but a shared guiding principle for the entire organization. In this blog we’ll open up our quality processes related to traceability and segregation in Sulapac production.
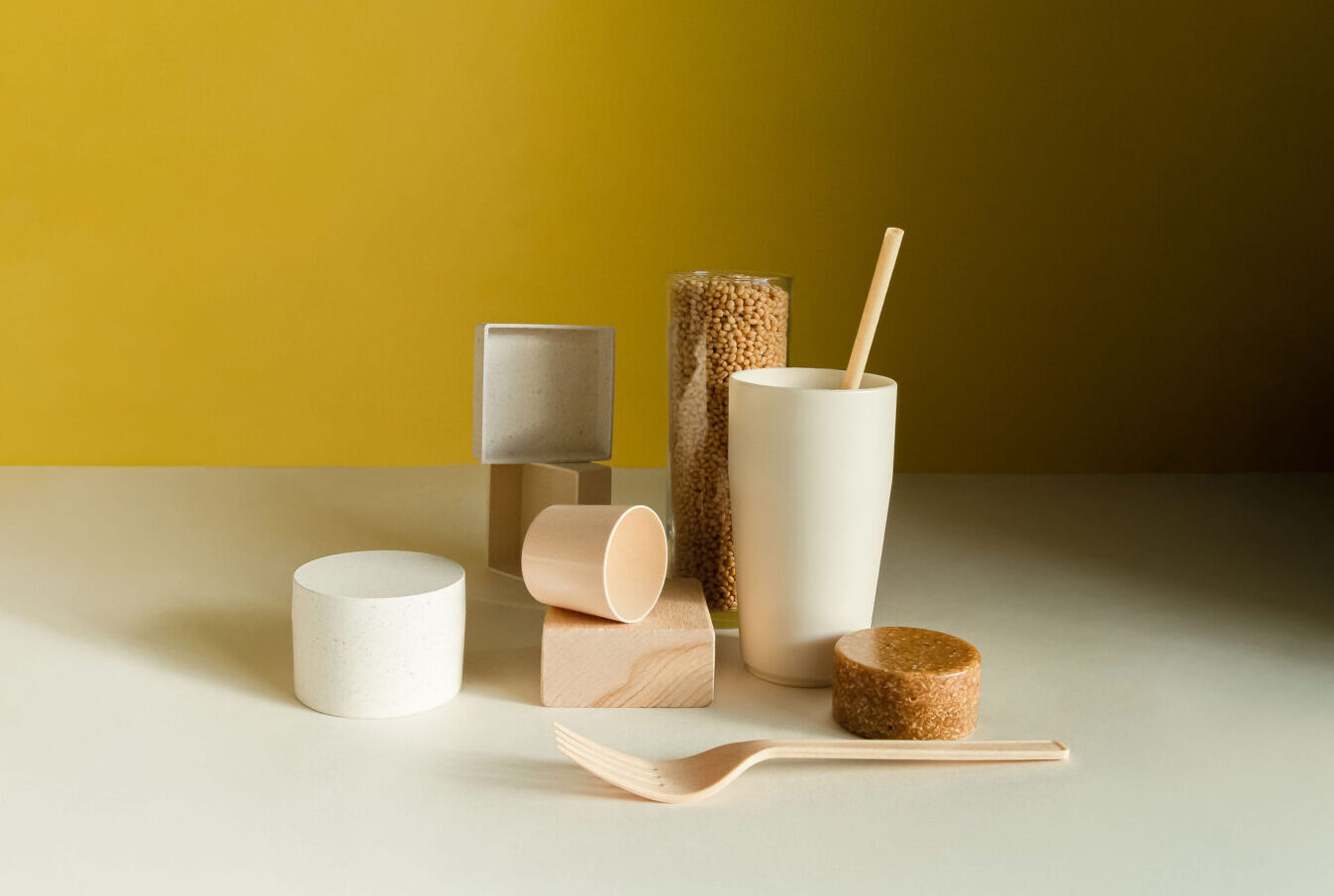
All Sulapac materials are produced as compliant with requirements of European Union regulation (EU) No 10/2011 on plastic materials and articles intended to come into contact with food and therefore they always fulfill statutory purity and traceability requirements.
Why standardized processes for traceability, segregation and raw material selection are important
Selection, traceability, and segregation of raw materials are critical aspects of quality control at Sulapac as they ensure that the raw materials used in the production of our materials meet specified standards, can be traced back to their source, and are handled in a way that prevents contamination or mixing of different ingredients.
When it comes to materials and articles intended to come into contact with food, the EU regulation (EU) No 10/2011 requires them to meet detailed criteria for traceability (as specified in article 17 of (EC) No 1935/2004):
1. The traceability of materials and articles shall be ensured at all stages in order to facilitate control, the recall of defective products, consumer information and the attribution of responsibility.
2. Business operators shall have in place systems and procedures to allow identification of the businesses from which and to which materials or articles are supplied. That information shall be made available to the competent authorities on demand.
3. The materials and articles which are placed on the market in the Community shall be identifiable by an appropriate system which allows their traceability by means of labelling or relevant documentation or information.
Sulapac’s manufacturing fulfils the requirements of the directives and regulations mentioned. We only subcontract production from companies, whose standard operating procedures already include raw material segregation and traceability as built-in features. Sulapac as well as our subcontracted manufacturers are ISO 9001 certified.
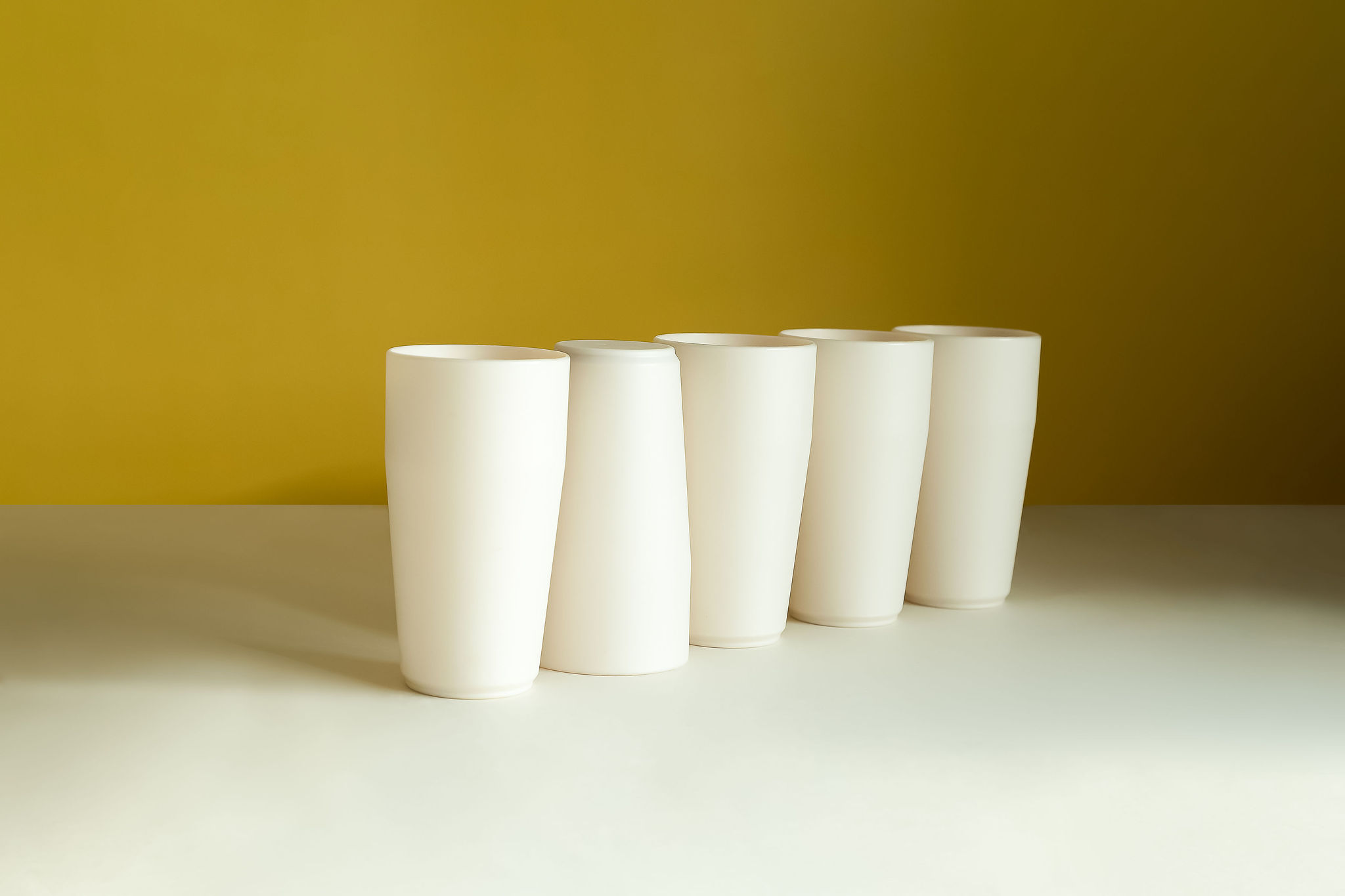
Raw material selection and evaluation
Prior to acceptance to production use, we evaluate all raw materials through our Raw material evaluation process, to ensure they fulfil the specific requirements for intended application. In practice this means that we request the necessary information and documentation from the supplier, carefully go through them and check them against our requirements. We also request a material sample, on which we conduct various preliminary tests. Once the regulatory evaluation has been completed and preliminary technical tests passed, the new raw material is accepted to proceed with further testing and development activities.
Raw material reception at storages
Each raw material is inspected on arrival at storages, to ensure condition and correctness of delivery and to record traceability information. On arrival the following is inspected:
– Name of the raw material
– Delivery documentation and quantity, including correctness of material references
– Batch number(s)
– Condition of packaging: eg no holes or leakages
– With certified materials, such as FSC or recycled materials, correctness of labelling according to standards’ requirements
As minimum, the following information of the incoming raw material is recorded in the resource planning system (ERP):
– Batch number(s)
– Date received
– Quantity received
– Expiration date (where applicable)
Delivery documentations are saved in our records and kept for minimum of 5 years.
If any defects, such as broken packaging or discrepancy of information attached to the delivery, are noticed in the incoming inspection, we evaluate the defect, including usability of the material in case of damaged packaging. The necessary steps are then taken to enquire with or inform the supplier as applicable, and to make the final decision on whether the material can be accepted for production or not. Any rejected materials are quarantined and later either returned to the supplier or disposed of.
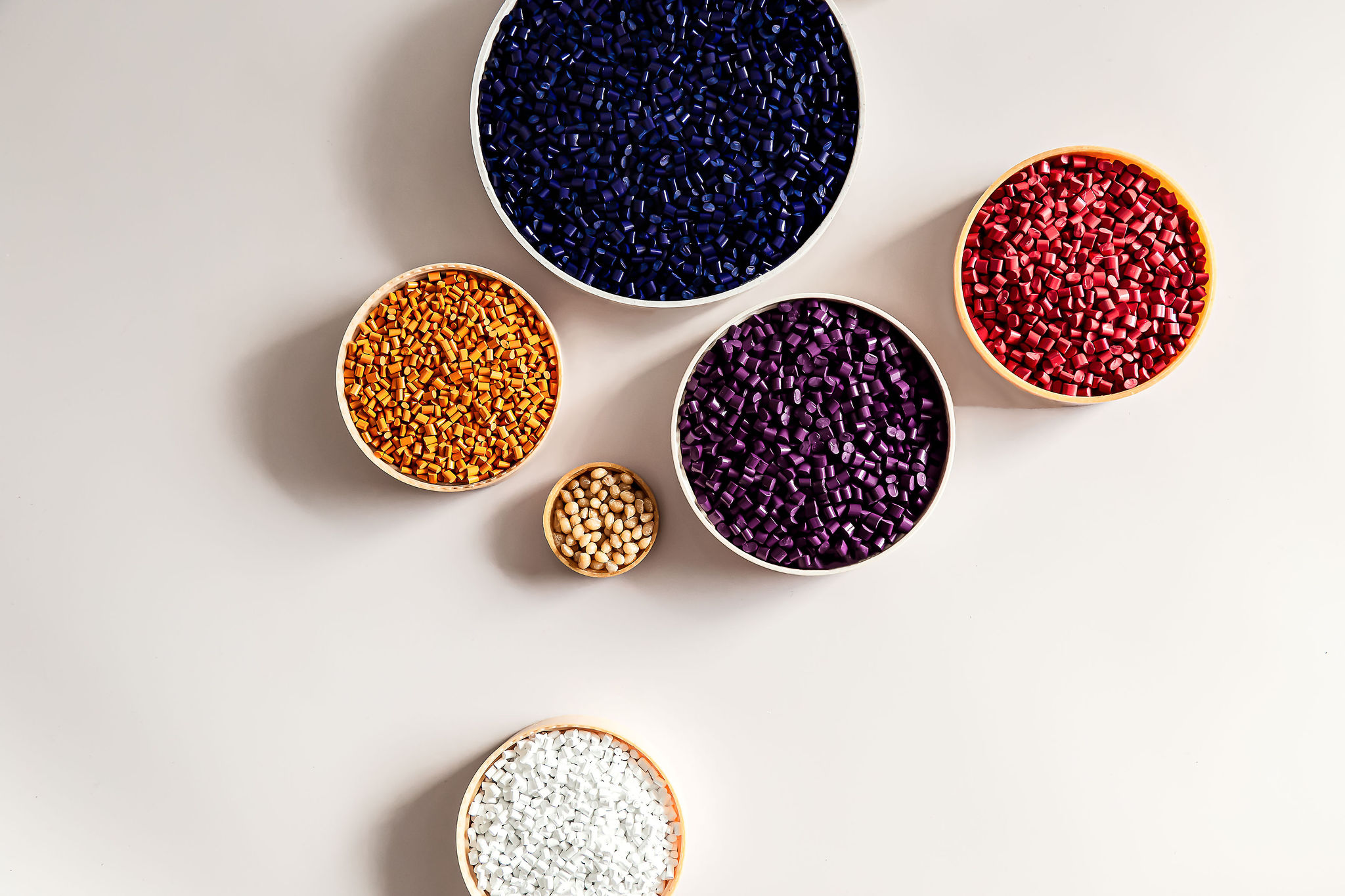
Raw material segregation and traceability in storage and production
European food contact regulations are strict against impurities and contaminants entering food contact material production, including raw materials used. Our manufacturing implements either HACCP (Hazard Analysis and Critical Control Point) method or equivalent in their production and storages. In addition, Sulapac materials are manufactured in accordance with Good Manufacturing Practice as described in (EC) No 2023/2006 on good manufacturing practice for materials and articles intended to come into contact with food, as required by (EU) No 10/2011.
Raw materials are stored in recorded storage locations, in their original packaging and in case of partially consumed packages, closed and secured against contamination. As standard procedure, we carry out monthly inventory checks, in order to maintain accurate data on raw materials and ready-made Sulapac materials in our storages.
For each Sulapac material batch produced, we have raw material consumption records, which always contain raw material names, batch numbers of raw material batches used, and quantities as kg or % of materials consumed. Once the production is ready, the correctness of raw materials is checked against the material recipe and the consumption of each raw material and batch(es) is recorded on entry to our ERP. The produced Sulapac material batch is checked by our quality department against quality specifications. Only after these checks have been completed and accepted, the Sulapac material is released for sale.
Through the records kept of our production batches, all Sulapac materials are fully traceable in terms of raw material batches used.
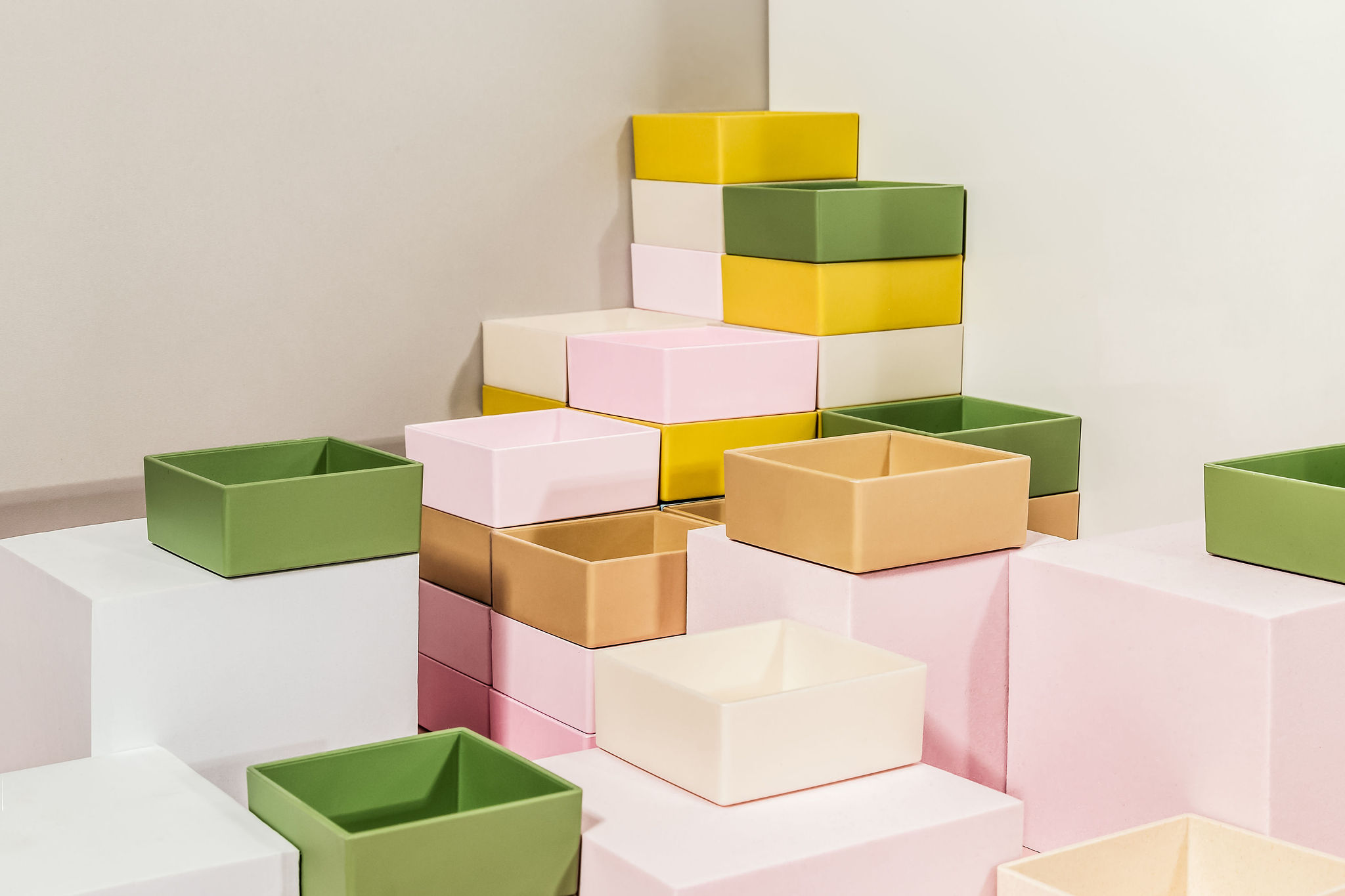
Traceability and segregation of compounded Sulapac materials
Besides full traceability in terms of raw materials, we have full forward traceability of compounded Sulapac materials: We keep record on to which customers each material batch has been sent, which is important in terms of ensuring consumer safety in cases where a contamination may have taken place, as it enables full recalls.
Sulapac materials are stored in recorded storage locations, in their original, sealed packaging, until they are shipped to the customers. Records of storage quantities and locations are kept in an identical manner as with raw materials.
Continuous improvement
As required by Finland’s legislation for food contact material manufacturers, we conduct an annual recall rehearsal which includes a full traceability exercise both forward and backwards. This not only fulfils the legal requirements but enables our continuous improvement efforts when it comes to traceability and record keeping.
In accordance with ISO 9001’s requirements, we implement a non-conformity procedure. This means that when something has not gone by the book, we conduct a root cause analysis, as well as take corrective and preventive actions. If the mistake is found to originate from the subcontractor, we expect a root cause investigation and preventive action measures to be reported back. All reported non-conformities are thoroughly investigated so that we can be sure to guarantee a stable, premium quality for our customers day in, day out.
If you have any questions about quality assurance at Sulapac, don’t hesitate to contact your account executive!